Nos actus
COMMUNIQUÉ DE PRESSE
Le Groupe Dürr élargit sa gamme destinée aux fabricants de batteries et se lance sur le marché du revêtement à sec
Bietigheim-Bissingen, Novembre 20, 2023 – Le Groupe Dürr a élargi sa gamme dans le secteur en plein essor de la technologie de production d’électrodes de batteries pour y inclure une technologie efficace et durable, orientée vers l’avenir. L’acquisition de la société d’ingénierie française Ingecal permet à Dürr de fournir dorénavant des systèmes de calandrage au secteur des batteries. Ces systèmes jouent un rôle crucial dans le revêtement des feuilles d’électrodes pour les batteries lithium-ion. En outre, Dürr a conclu un partenariat avec l’expert en revêtement américain LiCAP Technologies. Avec Ingecal et LiCAP, Dürr dispose d’un savoir-faire unique en production d’électrodes et peut maintenant proposer à ses clients non seulement le revêtement par voie humide, mais aussi une technologie de pointe en matière de revêtement à sec. Ce processus offre des avantages considérables au niveau des coûts, de la consommation d’énergie et des émissions de CO2 et peut aussi servir à la production des futures batteries à électrolyte solide.
Lors de la production d’électrodes, de fines feuilles de métal sont recouvertes de matériaux cathodiques et anodiques, constitués de produits chimiques. De nos jours, cela se fait normalement à l’aide de solvants. Toutefois, il est également possible d’appliquer un matériau sec sans solvants nocifs. Il s’agit d’une option très attrayante, tant sur le plan économique qu’en matière de durabilité, car le revêtement à sec nécessite jusqu’à 40 % d’énergie en moins et environ 20 % de temps de traitement en moins. De plus, les émissions de CO2 sont réduites d’environ 1 tonne pour tous les 10 kilowattheures de capacité d’électrode produite.
Ingecal, implantée près de Lyon et qui fait partie du Groupe Dürr depuis le 17 novembre, est spécialisée dans la technologie de calandrage. Lors de ce processus, les matériaux de la cathode et de l’anode sont pressés sur la feuille sous haute pression, à l’aide de deux rouleaux en acier. Les systèmes de calandrage de l’entreprise française conviennent aussi bien au revêtement par voie humide qu’au revêtement à sec. Ingecal, acquise par Dürr, est l’entreprise principale du Groupe Amalis qui réalise un chiffre d’affaires d’env. 15 millions d’euros et compte près de 70 employés. Le prix d’achat se base sur la valeur de l’entreprise plus une composante liée aux performances. Ces dernières années, Dürr et Ingecal ont coopéré avec succès sur plusieurs projets avec des fabricants de batteries et des constructeurs automobiles.
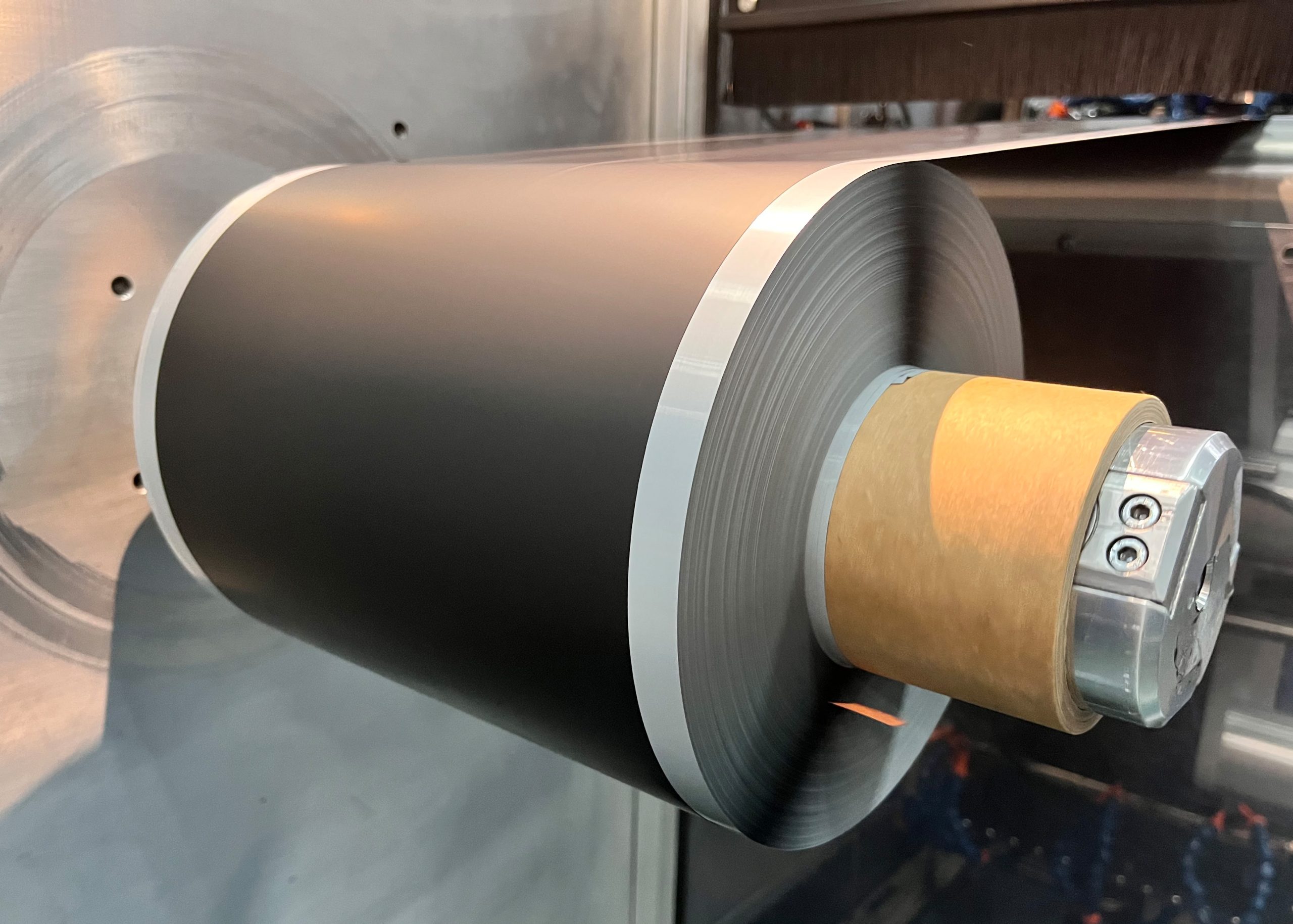
Dürr a conclu un partenariat avec l’expert américain en revêtement LiCAP Technologies. Ce partenariat vise spécifiquement l’enduction à sec des feuilles d’électrodes pour les batteries lithium-ion.
Le partenariat avec LiCAP Technologies se concentre spécifiquement sur le revêtement à sec. La société originaire de Sacramento (Californie) possède un vaste savoir-faire en ce qui concerne les matériaux utilisés et les exigences relatives au processus de revêtement. Le processus breveté Activated Dry Electrode® est l’un des fruits du développement réalisé par LiCAP et doit maintenant être lancé sur le marché en collaboration avec Dürr. Dürr et LiCAP sont déjà en pourparlers avec un fabricant renommé de cellules de batteries pour la construction d’une ligne de revêtement à sec.
De bonnes opportunités de croissance grâce à l’électromobilité
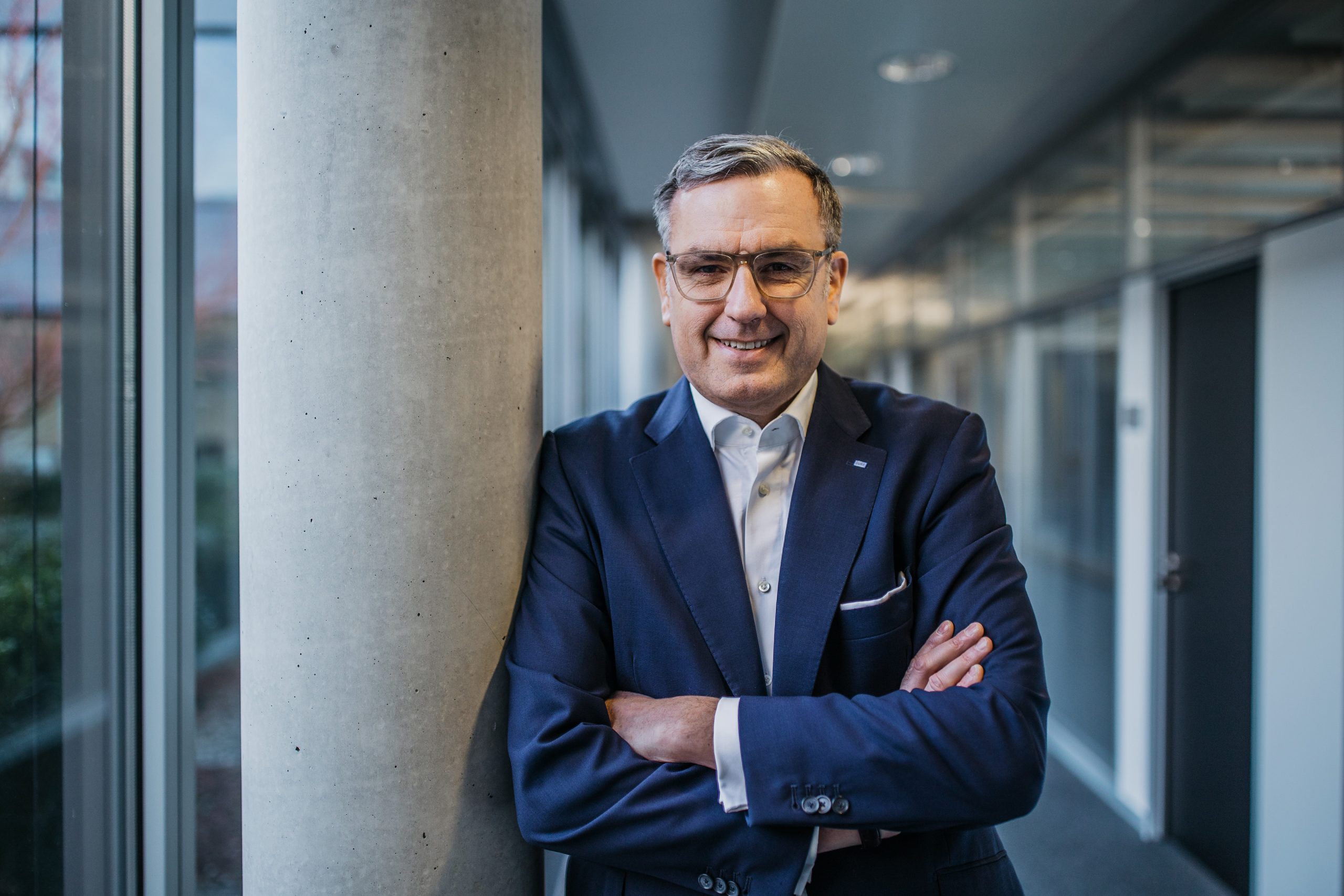
Dr. Jochen Weyrauch, CEO de Dürr AG
Dr. Jochen Weyrauch, PDG de Dürr AG, a déclaré : « Compte tenu du plein essor de l’électromobilité et de la tendance au stockage décentralisé de l’énergie, la technologie de production des batteries est l’un des domaines d’activité les plus importants du Groupe Dürr en matière de croissance. Avec Ingecal et LiCAP, nous proposons à nos clients une gamme complète de produits pour la fabrication d’électrodes et nous sommes également bien positionnés sur le marché d’avenir du revêtement à sec. Ingecal et LiCAP sont des partenaires hautement spécialisés, disposant d’une expertise reconnue et d’une excellente réputation dans le secteur des batteries. Ensemble, nous pouvons faire encore mieux et cela concerne aussi la fabrication de grands systèmes de revêtement destinés à des usines géantes de cellules.
L’élargissement de la gamme de produits de Dürr profite également à la coopération qu’elle a mise en place avec les entreprises d’ingénierie mécanique Grob et Manz depuis un an. Celle-ci vise principalement à fournir un équipement clé en main pour des usines géantes complètes. « Nous proposons désormais des systèmes de calandrage provenant d’une seule source et, ensemble, nous pouvons également cibler les clients qui dépendent du processus à sec lors de la première étape de la production d’électrodes », déclare Dr. Jochen Weyrauch. En outre, grâce à son savoir-faire en revêtement à sec, Dürr dispose d’ores et déjà d’une grande expertise en production de futures batteries solides. Celles-ci possèdent des électrolytes solides, contrairement aux batteries lithium-ion qui dominent actuellement.
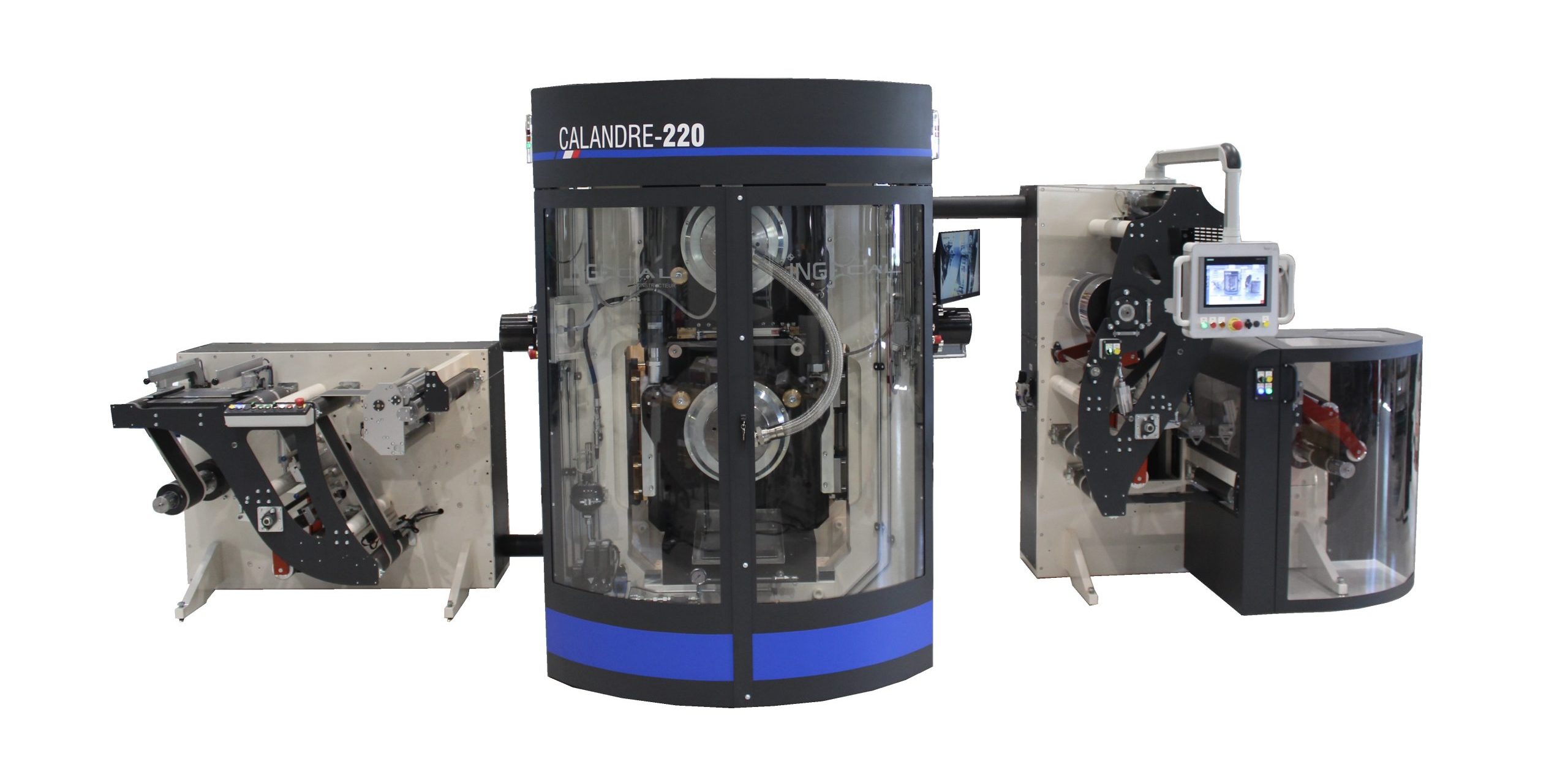
Grâce à l’acquisition de la société française d’ingénierie mécanique Ingecal, Dürr peut désormais fournir des systèmes de calandrage à l’industrie des batteries. Ces systèmes jouent un rôle clé dans le revêtement des feuilles d’électrodes pour les batteries lithium-ion.
À partir de 2030 environ, on prévoit que 30 à 40 % des électrodes de batteries fabriquées en Europe et en Amérique du Nord seront produites selon le processus du revêtement à sec. Néanmoins, le revêtement par voie humide restera un processus important. Actuellement, son développement vise principalement à remplacer les solvants NMP (N-méthyl-2-pyrrolidone) toxiques utilisés aujourd’hui par des solvants majoritairement inoffensifs. Pour le revêtement à sec, Dürr propose non seulement la technologie de revêtement, mais aussi des systèmes de séchage et de récupération des solvants. Dürr est d’ores et déjà l’un des principaux fournisseurs mondiaux de systèmes de récupération de solvants. Ils seront également nécessaires à l’avenir lors de l’utilisation de variantes de solvants inoffensifs.
Contact
- Dürr Systems AG
- Carina Lachnit
- Marketing
- Phone: +49 7142 78-4899
- E-mail: carina.lachnit@durr.com
- www.durr.com
A propos de Dürr
Depuis plusieurs décennies, le Groupe Dürr est représenté directement sur le territoire français et y emploie aujourd’hui près de 250 personnes. Les filiales françaises proposent la gamme complète des produits du Groupe : Dürr Systems S.A.S à Guyancourt opère principalement dans les domaines de la peinture et de l’assemblage, Dürr Systems à Lisses développe des technologies environnementales et fournit notamment des systèmes de purification de l’air pour les COV, les particules et autres émissions atmosphériques issues de procédés industriels. Dürr Systems à Lisses propose également des systèmes de revêtement pour électrodes de batterie lithium-ion. Les techniques d’équilibrage sont gérées par Schenck S.A.S. basé à Cergy Pontoise. En complément, Datatechnic S.A.S. à Uxegney propose des systèmes d’équilibrage spécifiquement dédié à la production des turbocompresseurs. Le groupe HOMAG construit des machines et des installations pour l’industrie de traitement du bois. En France, il est représenté à Schiltigheim par la société de vente et services HOMAG France.
Avec une solide expertise dans l’automatisation et la digitalisation/industrie 4.0, le groupe Dürr fait partie des leaders internationaux dans la conception et la réalisation de machines et d’installations. Grâce à ses produits, systèmes et services, les processus de production gagnent grandement en efficacité tout en économisant les ressources. Le groupe Dürr fournit principalement l’industrie automobile, les fabricants de meubles et de maisons en bois ainsi que les secteurs de la chimie, de la pharmacie, des appareils médicaux de l’électrotechnique et de la fabrication de batterie. En 2022, le groupe a réalisé un chiffre d’affaires de 4,3 Milliards d’Euros. Présent dans 32 pays, le groupe compte 20 500 salariés répartis sur 140 sites et opère sur le marché avec cinq divisions :
- Paint and Final Assembly Systems : Ateliers de peinture et technologie d’assemblage, de test et de remplissage de fluides pour l’industrie automobile, systèmes d’assemblage et de test pour les dispositifs médicaux
- Application Technology: Technologies robotiques pour l’application automatique de peintures ainsi que de produits d’étanchéité ou d‘adhésifs
- Clean Technology Systems : Installations pour le traitement des effluents gazeux, équipements pour dépôt de revêtements sur batterie lithium-ion et systèmes antibruit
- Measuring and Process Systems : Systèmes d’équilibrage et technologie de diagnostic
- Woodworking Machinery and Systems : Machines et systèmes pour l’industrie de transformation du bois
Ils parlent de nous...
ALINE NIPPERT
Publié le 13/04/2021
« La ligne pilote d’ACC à Nersac produira les premières batteries lithium-ion en novembre-décembre », avance Olivier Dörr, directeur industriel d’ACC
Automotive Cells Company (ACC), qui fait partie des principaux bénéficiaires du premier IPCEI (Important Projects of Common European Interest), a officialisé son lancement à l’été 2020. La coentreprise entre Saft (filière de Total) et Stellantis (ex-PSA), parfois surnommée l’ « Airbus de la batterie », a ainsi reçu près de 1,3 milliard d’euros de fonds publics allemands et français pour implanter deux gigafactories, dans les Hauts-de-France ainsi qu’en Rhénanie-Palatinat (Allemagne). Alors qu’un deuxième « Airbus des batteries » a été lancé fin janvier 2021, le directeur industriel d’ACC, Olivier Dörr, revient sur l’avancement de leur projet industriel pour Industrie & Technologies.
Et affiche des ambitions fortes.
[…]
L’ « Airbus des batteries » a pour ambition de développer une filière industrielle des batteries que le Vieux-Continent. Vos appareils industriels sont-ils européens ?
Nous poursuivons deux objectifs : celui d’être européen certes, mais aussi celui d’être compétitif. Si, pour Douvrin les choix ne sont pas encore arrêtés, la majorité de nos machines-outils à Nersac proviennent d’Asie… Comme les batteries sont aujourd’hui fabriquées sur ce continent, ce sont les acteurs asiatiques qui maîtrisent les outils de production. Ainsi l’essentiel de notre ligne est fourni par un consortium germano-chinois, la partie chimie est coréenne, la partie formation et assemblage est chinoise. Nous avons toutefois un fournisseur français, Ingecal, pour notre machine de calandrage et échangeons avec des acteurs européens.
[…]
Depuis de nombreuses années Ingecal fabrique des équipements pour le secteur des composites.
Nos lignes d’imprégnation, filmeuses, stations de refente, lignes de poudrage et de visite équipent aujourd’hui des industriels tels que Airbus, Ariane, Hexcel, Arkema, Eurocpter, Duqueine, Porcher, …
En 2019 Ingecal a été sélectionné pour développer et créer une ligne de fabrication de composites Carbonne thermoplastiques (PEKK) dans le cadre du projet HAICOPAS
HAICoPAS(*) : Projet de développement d’une nouvelle filière de composites pour applications structurales destinées aux marchés Aéronautique, Automobile et Oil & Gas intégrant des nappes Carbone à matrices Thermoplastiques Hautes Performances.
Le projet de Recherche et Développement HAICoPAS (porté par un consortium d’industriels, d’académiques et soutenu par un financement étatique BpiFrance) s’inscrit dans la mise en place d’une nouvelle chaîne de valeur « matériaux et procédés » qui permettra, à terme, d’alimenter une nouvelle filière de solutions complètes en matériaux composites Carbone / Thermoplastique destinées aux structures primaires et travaillantes, utilisées dans les marchés aéronautiques, automobiles et oil & gas. Les finalités du projet HAICoPAS (Highly Automatized Integrated Composites for Performing Adaptable Structures) consistent à lever un certain nombre de verrous technologiques afin d’optimiser tout le processus depuis la conception et la fabrication des nappes Carbone / polymères Thermoplastiques Hautes Performances (PEKK, PAHT, PVDF) à la production de pièces composites ; à un coût compétitif et cadence élevée. Ce projet ambitionne également de développer une technologie de placement de nappes découpées (« slit » tape) plus productive ; de même qu’un nouveau système d’assemblage de pièces finales par soudage (ISW) avec contrôles non destructif et dimensionnel qualité en ligne.